Improving surface quality for sustainable manufacturing
3D printing, or additive manufacturing (AM), has developed vastly over the past years and is already a well-used alternative when producing plastic and metal parts for a range of different products. However, there is still a great need for improving surface quality in order for 3D printing to eventually replace conventional manufacturing techniques and contribute to the necessary shift towards sustainable manufacturing. Amogh Vedantha Krishna, PhD student at Halmstad University and Chalmers University of Technology, has recently presented new research findings for surface improvement in additive manufacturing.
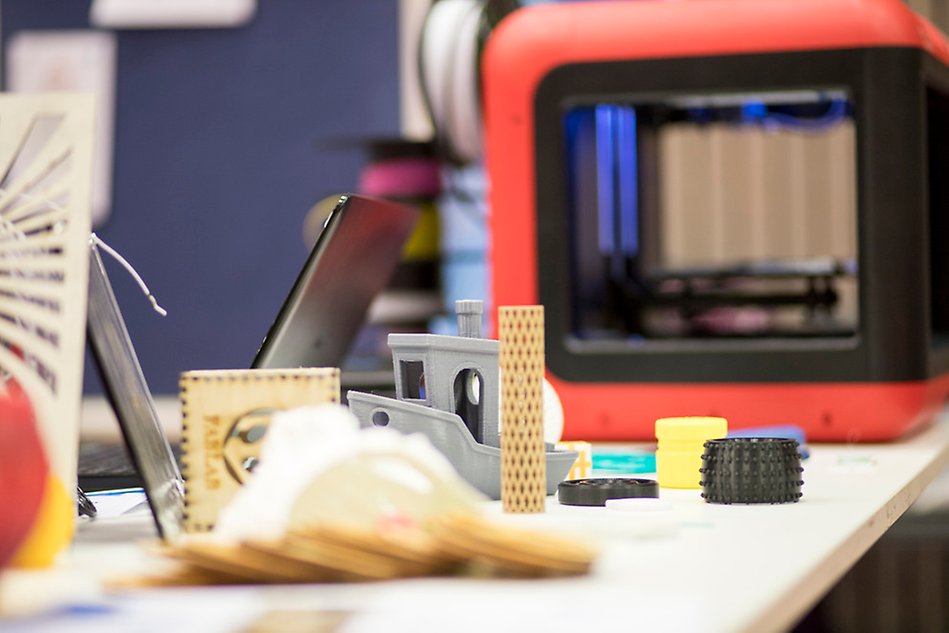
“Additive manufaturing can be a complement to traditional manufacturing methods and a vital part of the shift towards sustainable production.”
Amogh Vedantha Krishna
Additive manufacturing is a technique where three-dimensional objects are created with precision by building them layer by layer. A simple way of describing the technique is that melted material, for example plastic or metal, is deposited through a printer nozzle one layer at a time. The nozzle movement is controlled by a computer programme following the exact design of the object. The advantages of AM, also known as 3D printing, compared to conventional manufacturing methods are for example better customisation, the possibility to manufacture light-weight parts, no assembly requirements, reduced wastages, lower energy intensity as well as reduction of lead time, manufacturing costs and time-to-market. Many of these advantages lead to sustainable benefits.
“Additive manufacturing, AM, has the potential to replace conventional manufacturing processes, provided that the disadvantages are handled – for example quality issues and difficulties for mass production. Until these problems are solved, AM can still be a complement to traditional manufacturing methods and a vital part of the shift towards sustainable production”, says PhD student Amogh Vedantha Krishna who recently published his licentiate thesis on quality assurance of AM parts.
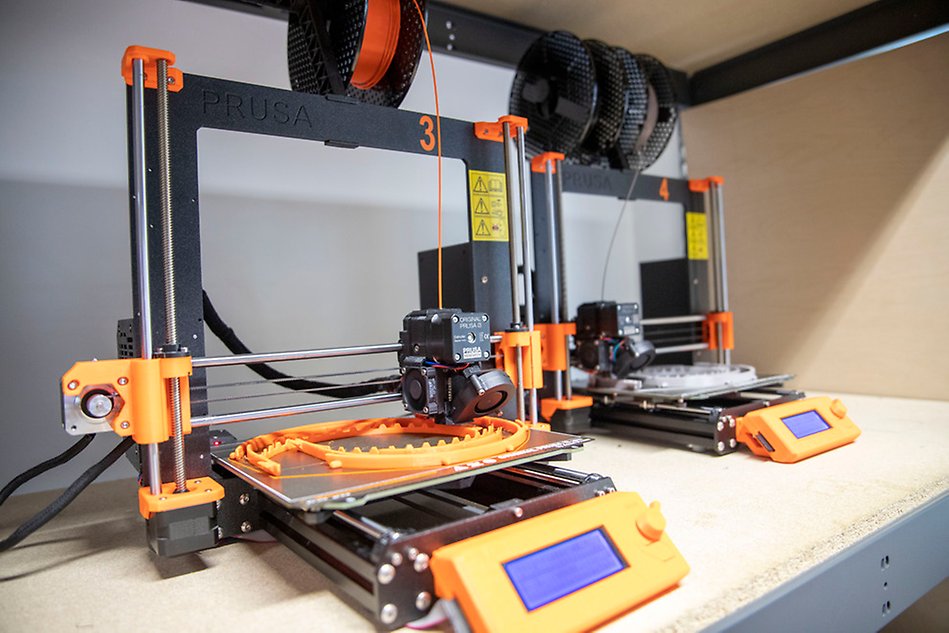
This is a picture of a 3D printer, more specifically a Fused Deposition Modeling (FDM) machine, at Fab Lab at Halmstad University. In his research, Amogh Vedantha Krishna has studied additive manufacturing (AM) of both plastics and metals. The AM technology he used for plastics is FDM. For metallic materials, Amogh Vedantha Krishna used a laser-based powder bed fusion, also known as Selective Laser Melting. Fab Lab at Halmstad University has FDM machines for plastics and Chalmers University has the metal printers.
Fab Lab for research and creative development
Fab Lab at Halmstad University is a creative centre with a focus on free-form production and 3D printing. At Fab Lab, the University’s researchers and students work on developing materials and manufacturing methods, often in collaboration with industry. One of the research groups working at Fab Lab is the material systems group within the research environment Rydberg Laboratory for Applied Sciences (RLAS). Amogh Vedantha Krishna is a PhD student at Halmstad University and Chalmers University of Technology, working in the material systems group with research specifically on the surface quality of products produced by AM.
“Although AM has several advantages, one of the main downsides of this technique is the surface quality. Surface defects can influence the functional performance of the manufactured parts and cause significant failures if left unchecked. The focus of my research is to improve the surface quality of products produced by AM to match the standards set by conventional manufacturing processes, for example milling, turning and injection moulding. By doing so, more industries can use AM technology in their supply chain”, says Amogh Vedantha Krishna.
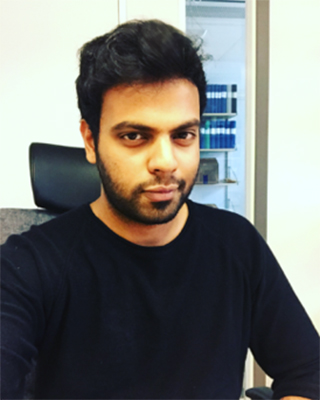
“In my research, a methodology was developed to identify the most critical surface features that are affected by the AM process settings and other variables. By studying these surface features, it is possible to understand the manufacturing process and to enable process control and optimisation of surface quality”, says Amogh Vedantha Krishna, PhD student at Halmstad University and Chalmers University of Technology.
Why is surface quality so critical?
It is very important to control the surface quality, especially in high-end precision applications, where the nature of the surface plays a major role in the functional performance of the part. For other application areas, where the surface does not affect the function of the part, the surface quality might not be as crucial, making AM easier to implement as a manufacturing method. One example of when the surface quality is highly important is for parts in an engine, more specific a piston and cylinder. A layered surface produced by AM can lead to high wear rate – more friction – between the piston and the cylinder, ultimately causing a failure in the engine. A too smooth surface can on the other hand also be a problem as it may not hold necessary lubricant, which can also cause high friction and engine failure.
“In this case, an engineered surface that is comparatively smooth but has some groves to hold lubricants is required. This can be achieved by improving the surface of an AM printed part after it has been created, so-called post-processing. In this way, the surface can be manufactured to maximise efficiency and functionality of the part in an engine. This is not a case that I have worked with, but it is a good example to illustrate the importance of surface quality”, says Amogh Vedantha Krishna.
The choice of post-processing method depends on the nature of the surface and material as well as on the design of the final product. Amogh Vedantha Krishnas research focuses on which post-processing method is the best possible choice to improve the surface quality of a specific product.
“I have evaluated the post-processing methods based on the cost, time, geometry and function of the polymer products specific to an AM technology called Fused Deposition Modeling (FDM). My research showed that the extra incurred costs of post-processing can be compensated by re-designing the models to reduce the manufacturing time and material usage”, says Amogh Vedantha Krishna.
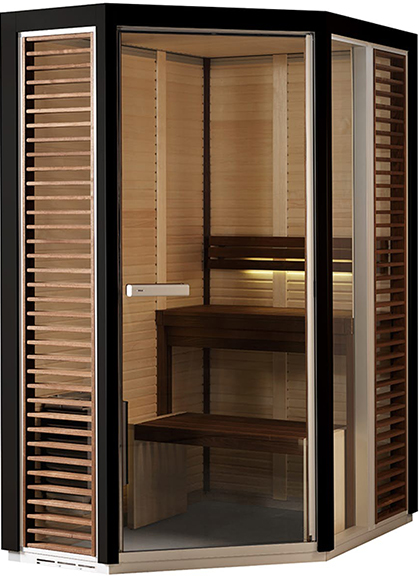
Amogh Vedantha Krishna has worked together with the sauna company TylöHelo, to help them improve the visual appearance of AM produced parts. Picture: TylöHelo
Collaboration with TylöHelo
There are many other examples, besides the engine case above, where surface quality is important. Amogh Vedantha Krishna has worked together with sauna company TylöHelo to help them improve the visual appearance of AM produced parts. This was done by using post-processing methods, which significantly improved the aesthetic properties of polymer parts produced by AM technology. However, it increased the cost per part due to the additional processing steps.
“TylöHelo wanted to use AM to enable customisation. At the same time, they required quality and cost to be as good as using injection moulding (IM) as manufacturing method”, says Amogh Vedantha Krishna.
The additional costs for post-processing were reduced by using a mathematical method called Topology Optimisation for re-designing parts to reduce material usage while retaining or maximising functional performance.
“The capability of AM to produce the Topology Optimised parts compared to conventional manufacturing processes is remarkable”, says Amogh Vedantha Krishna.
By employing post-processing methods and Topology Optimisation, it was possible to come close to the quality and cost set by the IM process. This encouraged TylöHelo to set up an AM machine for manufacturing their sauna parts which were earlier produced by the conventional IM method.
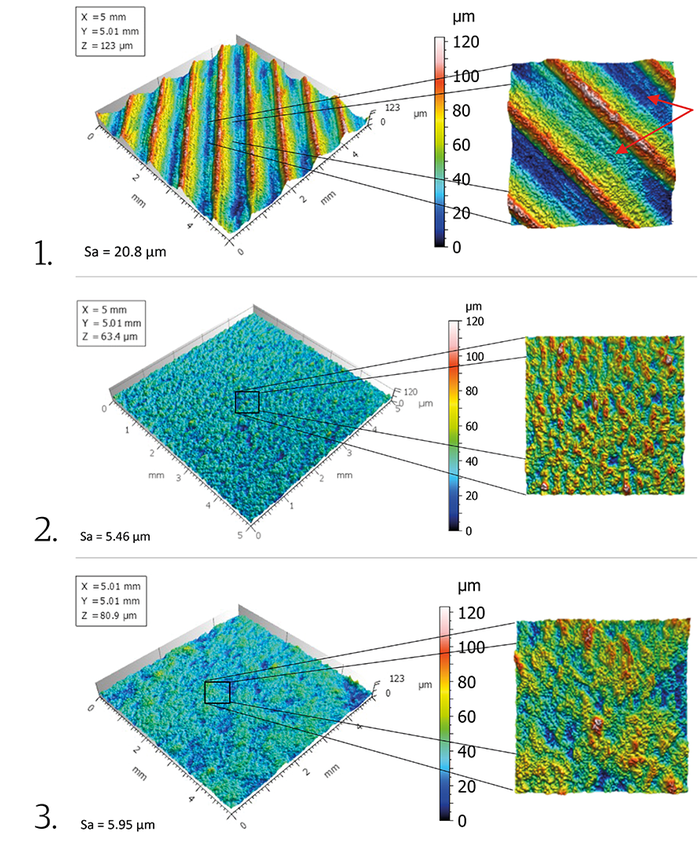
The surface of Fused Deposition Modeling parts (image 1) after post-processing through shot blasting (image 2) have similar features to a product produced by Injection Moulding (image 3). It can be observed visually in surface images and also from the Sa value, which is the average area roughness parameter.
Future possibilities
Additive manufacturing (AM) is important for industries because it has several sustainability advantages compared to other manufacturing methods, for example, reduced wastage and energy consumption. These advantages are enabled mainly due to the specific technology of AM where objects are built by selective and progressive deposition of material, layer by layer. On the question if a movement towards more AM will change the global manufacturing world in the future, Amogh Vedantha Krishna answers:
“At the moment, for high-end applications, other manufacturing technologies are preferred until the disadvantages for AM, for example surface quality, is solved. For that reason, I think companies that have existing traditional or conventional manufacturing systems will not replace them with AM but would want to include AM in their supply chain to tackle customisation. At the same time, they can create new markets as well. However, there are many companies who are moving from the concept of mass production to mass customisation and in such cases, AM can be a one-stop solution”.
The future for Amogh Vedantha Krishna will hopefully be within research:
“I have grown fond of what I am doing at Halmstad University, so after my doctoral education I would like to stay within the academic field. Hopefully, I will get an opportunity here in Halmstad. If not, my second option would be to work at a research institute, like RISE”.
Text: Louise Wandel
Photo: Ida Fridvall, Linnéa Andersson and TylöHelo
About the licentiate thesis
The overall aim of the licentiate thesis Towards Topography Characterization of Additive Manufacturing Surfaces by Amogh Vedantha Krishna is to establish the most effective approach towards topography characterisation of Additive Manufactured surfaces to facilitate a better understanding of the manufacturing process for enabling process control and optimisation of surface quality.
“This thesis focuses on improving the understanding of the manufacturing process and enabling process optimisation to enhance the surface quality and part function, thereby, helping the industries to implement additive manufacturing into their supply chain”, says Amogh Vedantha Krishna.
Thesis title: Towards Topography Characterization of Additive Manufacturing Surfaces External link, opens in new window.
School of Business, Innovation and Sustainability (FIH) at Halmstad University.
The Department of Industrial and Materials Science at Chalmers University of Technology.
Subject: Material Science
Supervisor/Examiner: Bengt-Göran Rosén, Professor in Mechanical Engineering at Halmstad University
Opponent: Frédéric Cabanettes, Assistant Professor, Laboratory of Tribology and Dynamics of Systems (LTDS), Ecole Nationale d'Ingénieurs de Saint Etienne (ENISE)
The licentiate seminar was held on October 29, 2020, at Chalmers University of Technology in Gothenburg.
About Amogh Vedantha Krishna
Amogh Vedantha Krishna holds a Bachelor in Mechanical Engineering from Visvesvaraya Technological University in India. He worked for two years as a production engineer before coming to Sweden for a Master’s in Mechanical Engineering at Halmstad University.
“My master thesis helped me get a job as a research assistant at Halmstad University. I worked for two years doing various projects and in 2018, I got a PhD student position at Chalmers University in the same field as I did my master thesis and the work I did as a Research Assistant. Although I am a Chalmers PhD student, I identify myself as a Halmstad University PhD student as most of my work is at Halmstad University under the supervision of Professor Bengt-Göran Rosén”, says Amogh Vedantha Krishna.
Read more
The research project DiSAM where Amogh Vedantha Krishna is active:
Digitisation of the production flow of additive manufacturing in Sweden (DiSAM)
The project DiSAM lies within the research environment RLAS at the School of Business, Innovation and Sustainability (FIH) at Halmstad University:
Rydberg Laboratory for Applied Sciences (RLAS)
School of Business, Innovation and Sustainability (FIH)
Amogh Vedantha Krishna is admitted as a PhD student at Chalmers:
Sustainable manufacturing research is well in line with Halmstad University profile area Smart Cities and Communities:
Profile area Smart Cities and Communities
Artikel på svenska:
Förbättring av ytans kvalitet för ökad hållbar tillverkning External link.